A Guide to Understanding Horizontal Carousels
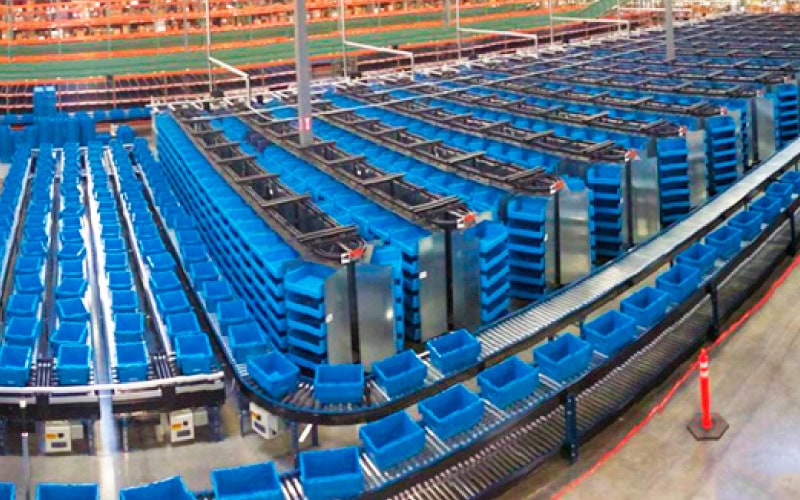
Maximize Storage & Efficiency with Horizontal Carousels
Learn how horizontal carousels help businesses solve space constraints, improve productivity, and streamline operations—plus how to choose the right one for your facility.
What’s Inside the Guide
What is a Horizontal Carousel?
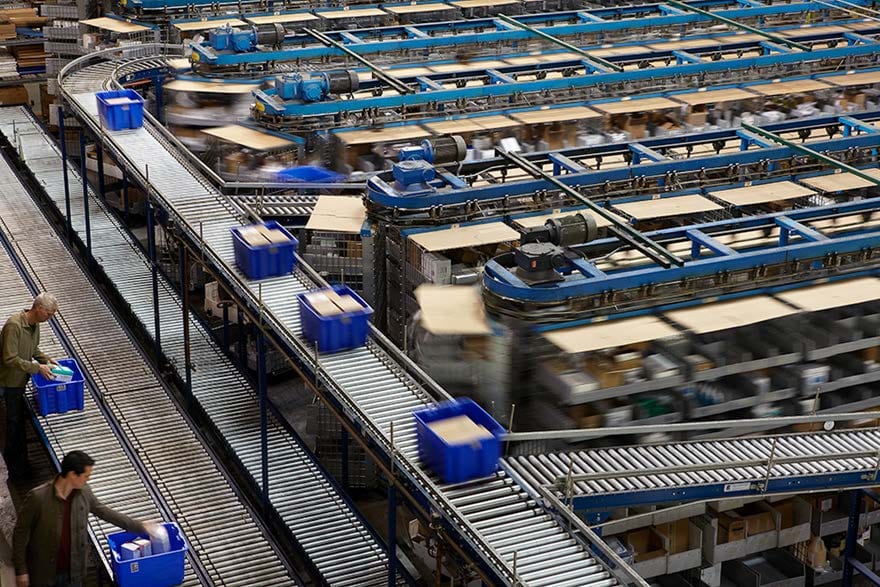
As the name implies, a horizontal carousel moves horizontally, similar to how a merry-go-round spins and most applications involve multiple units feeding each operator. Imagine two or three dry-cleaning carousels with baskets hanging from them, all bringing goods to the same operator. The operator can pick from multiple baskets simultaneously, usually directed by lights that indicate the right items and quantity. That means operators can pick hundreds of line items an hour and multiple work orders at one time.
Horizontal carousels have a wide range of applications
Horizontal carousels can be used for both internal and external distribution processes. For example, horizontal carousels can improve the efficiency, accuracy, and speed of internal kit making. They are also widely used inside manufacturing facilities for filling orders that are distributed externally to customers.
A brief history of the horizontal carousel
White Systems was founded in 1946 and by the 1960s, it was the world’s leading manufacturer of garment storage conveyors for dry cleaners, laundries, and apparel producers. In fact, most of the horizontal garment storage conveyor systems in use at dry cleaners even today were built by White Systems. Over time, the company evolved to use its conveyor mechanism to drive bins and totes for warehouse storage. These machines were the early versions of what we now know as horizontal carousel storage and distribution systems. The internal mechanisms of today’s horizontal carousels are integrated with computer systems to create sophisticated automated solutions for inventory management and distribution.
Horizontal carousels are in demand as e-commerce applications grow
The technology behind horizontal carousels is tried and true, and over the years, it has been adapted to a variety of new business environments. Most recently, there has been a surge in demand due to the rise of omni-channel distribution centers. These facilities serve as e-commerce hubs, shipping not only to stores but also directly to customers. That means that at omni-channel distribution centers, the volume of picks is increasing, while the order size is decreasing. At the same time, e-commerce retailers are judged by how fast, and how cost-effectively, they can fulfill orders and ship them out the door. Horizontal carousels are gaining in popularity because they can improve the efficiency, accuracy, and speed of inventory management and distribution.
[Take it with you. Download the Guide to Understanding Horizontal Carousels]
Alternatives to Horizontal Carousels
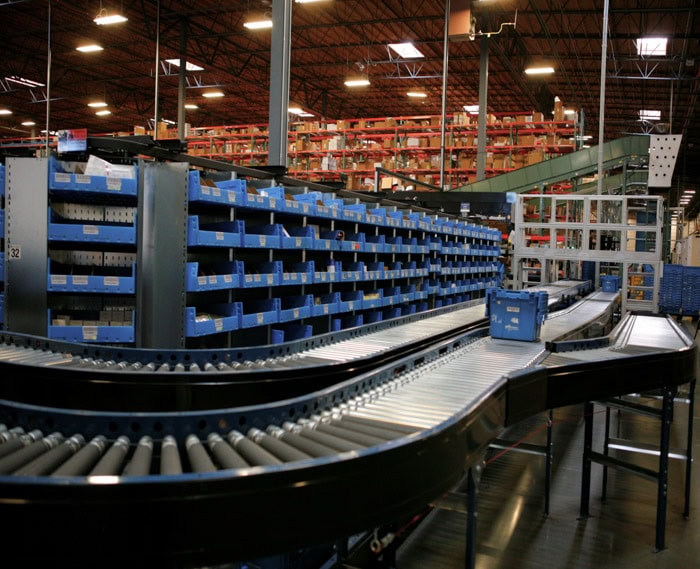
There are a variety of ways to store and manage inventory for internal or external distribution. Some of these methods, such as static shelving, are relatively low-tech. Others are more sophisticated, involving integrated computer applications and sometimes, robotics. This second group includes a variety of automated storage solutions—not only horizontal carousels, but also vertical carousels, vertical lift modules (VLMs), ASRS or shuttle systems, and grid systems.
Static shelving
Static shelving is one of the most commonly used methods of inventory storage and management. Its big advantage is the low initial cost. However, because the dimensions of static shelving units are fixed, they cannot be adjusted to optimize warehouse space. In addition, when inventory is stored on shelves, pickers have to walk up and down the aisles of the warehouse every time they need to fill an order. That takes time, is error-prone, and can be hard on pickers physically (with all the “pounding the pavement,” bending, and repetitive motion). Static shelving can also introduce safety hazards. After all, an operator can only pick as high as they can see—beyond that, they have to reach or use a ladder. Reaching and climbing ladders create risks, and both add even more time to the pick.
Vertical carousels
Vertical carousels are automated storage solutions that operate on the vertical axis. The mechanism that drives a vertical carousel is similar to the mechanism that drives a Ferris wheel; however, rather than rotating on a circular path, as a Ferris wheel would, the shelving units move up and down vertically, following an elongated oval path. This configuration means that vertical carousels have a small footprint on the warehouse floor and can more than double the storage capacity of ordinary static shelving units.
What we call “the footprint” is measured at the base of the unit. Typically, a vertical carousel is five to seven feet deep and 10 to 12 feet wide—although, at SencorpWhite, we can customize solutions to fit smaller niche spaces. When we are working with you to design a vertical carousel, we look at the square footage you currently are using for storage space and use that to help determine the pan depth, width, and height. The height can be variable, so if you are storing small items, we can make the shelves denser, and if you have tall items, we can make the shelves farther apart. This allows us to maximize storage density and minimize the footprint. Remember, usable storage is what fits on the shelves or in the pans. SencorpWhite has one of the smallest motor footprints in the industry, so the usable storage density is very near the overall cubic footprint.
Vertical carousels are becoming increasingly common across all sectors, in industries ranging from aerospace and manufacturing to retail and pharmaceuticals. That’s because in addition to increasing storage density, they can significantly improve warehouse performance. As with a horizontal carousel, a vertical carousel’s internal mechanism is integrated with computer software, creating a true “goods-to-person” delivery system. When a certain product needs to be picked, it is the software that directs the carousel to present the correct tote to the operator at the work counter. This accelerates pick speed, improves picking accuracy, and enhances workplace ergonomics.
Another advantage of SencorpWhite vertical carousels is that they include an emergency hand crank for manual backup. If there is a system failure, operators can release the brake and use the hand crank to turn the internal mechanism. They can empty or fill the whole device, enabling operations to continue until the unit is running fully automated again.
Vertical lift modules
Vertical lift modules (VLMs) are similar to vertical carousels in that they run vertically and present trays to an operator. The operator can look across the tray, pick the item needed, and then press a complete button so that tray is removed and the next one is delivered. VLMs typically have a greater weight capacity than vertical carousels, which makes them ideal for heavier items. Another advantage to SencorpWhite’s VLMs is that they are available in single column or multiple column formats. In fact, one SencorpWhite VLM can provide up to seven windows to pick from. In some instances, there are windows on the front and windows in the back, so that picking and replenishment can happen simultaneously.
Both vertical carousels and VLMs offer dynamic shelving and light-directed picking. When a tray is presented to the operator, a shutter comes down across the back. An image of the product is displayed on the shutter, along with where it’s located on the tray and other information, including SKUs, quantities needed, and updated inventory counts. On vertical carousels, all of this can be displayed on the marquee bar that’s in front of the operator.
Shuttle systems
Some automated storage and retrieval systems (AS/RS) use a shuttle, similar to an unmanned fork truck, to run back and forth between static shelving units. The shuttle is able to move vertically and horizontally, and it can be programmed to travel to a shelf and retrieve items. Generally, shuttle systems are used for internal or external distribution of full pallets or cases and for heavy items, such as motors or other parts needed in assembly processes.
Grid systems
Grid systems fit all of the inventory into totes within a standard, closed unit box. Then, a robot is programmed to pick the items that are needed. The key with a grid system that is every item must be able to fit within the grid. When that’s possible, they offer very dense storage capacity. To keep the stored items accessible to the robot, at the end of the shift, the next shift’s work is re-positioned within the grid so that the products needed most are located near the top. Think of this as somewhat similar to the way tiles can be re-positioned on a Rubik’s cube. Grid systems can run continually, optimizing slotting. They work best in warehouses that need to prioritize storage capacity, but not necessarily picking speed.
How different automated solutions compare on cost
Calculating the true cost of an automated system depends on the ROI and what storage and distribution problems you are trying to solve. For example, the grid system may be the most expensive, but it may have the least cost per square cubic foot. Then again, if vertical carousels and VLMs are sized properly, they can provide very dense storage, as well. Horizontal carousels are probably in the medium price range per cubic foot; however, the speed and accuracy of the picks can make them an optimal solution.
[Take it with you. Download the Guide to Understanding Horizontal Carousels]
The Many Business Benefits of Horizontal Carousels
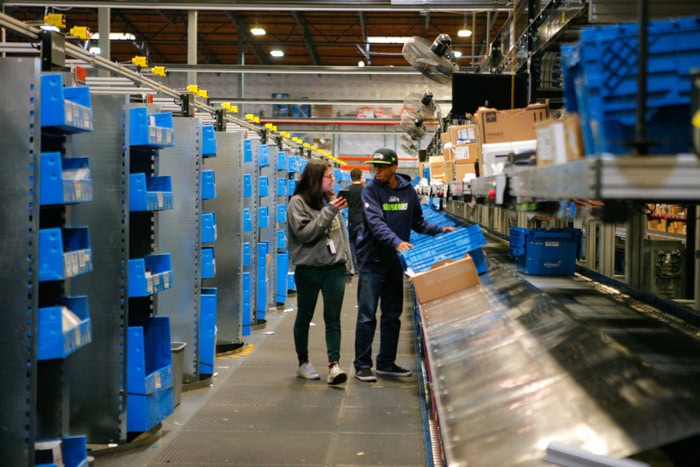
Horizontal carousels offer numerous business benefits, ranging from accelerating pick speed and improving picking accuracy to expanding storage capacity and better adaptability to times of peak demand. At SencorpWhite, we will work with you to deliver not just upfront ROI, but also long-term ROI relative to your cost of ownership.
Horizontal carousels improve picking efficiency
Horizontal carousels enable incredibly efficient picking, especially for medium weight items that are in the range of a few ounces to several pounds. The units can hold 75 pounds per shelf, and ideally, picks should be faster in the distribution and denser during the non-distribution. That enables 20 or more orders in the distribution, limited only by the amount of software. The orders can be placed ergonomically, so all the fastest moving SKUs are at about waist height for the operators. That way, most of the orders can be picked within minutes. SencorpWhite customer can typically pick 100-150 line arms without optimization. After we add in the right software and light-directed picking, that number can easily increase to more than 250.
Horizontal carousels accelerate picking speed without sacrificing accuracy
Horizontal carousels are among the fastest, if not the fastest, automated storage solutions. They also help operators make accurate picks. When product is stored in a horizontal carousel, similar items are not stored together. Instead, the shelves are divided into multiple cells, each with distinct, different-looking items to prevent mis-picks. In addition, with light-directed picking, an image of the needed item can be displayed, along with where it’s located and other information, including SKUs, quantities needed, and updated inventory counts. Put all of that together, and pick accuracy skyrockets. And improving pick accuracy results in real cost savings.
Horizontal carousels offer better adaptability to times of peak demand
Combining accelerated picking speed with improved accuracy makes it easier to respond to times of peak demand. Whether it’s a brick and mortar store or an e-commerce distribution center, customers tend to buy more (or less) at certain times. Internet shopping, for example, tends to peak between 7:00pm and 10:00pm. In manufacturing, the peak times could be from 10:00am to 3:00pm because that’s when people in purchasing get the orders from the floor. Horizontal carousels can help you cover these spikes in demand with picking that is fast and accurate.
Improved storage capacity and dynamic shelving
Horizontal carousels provide improved storage capacity because the shelving is dynamic. At SencorpWhite, we can put the shelves on two-inch centers, so for example, if you need dense and small product in an eight-foot carousel, we can put six shelves per foot for maximum density. For longer items, like and eight-foot item, the carousel can be reconfigured from six shelves to two shelves within minutes. That means you can adapt your horizontal carousel to accommodate seasonal or special products.
[Take it with you. Download the Guide to Understanding Vertical Carousels]
What Are the Components of A Horizontal Carousel And How Do They Work Together?
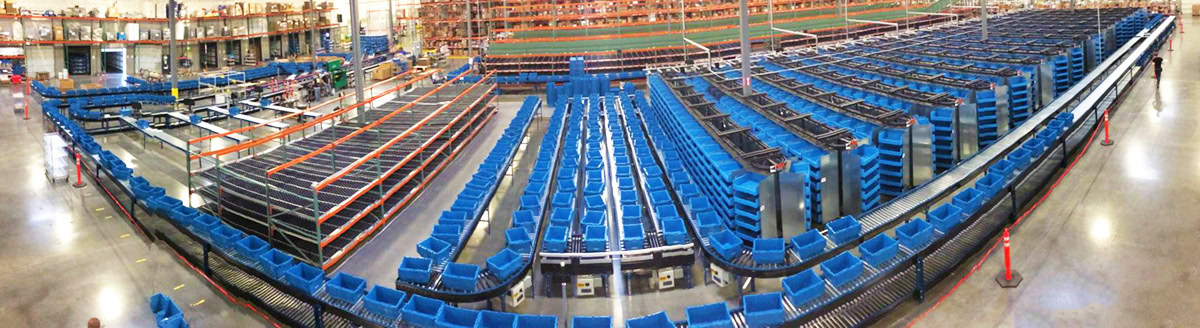
Horizontal carousels are generally assembled in groups of three or four. These are called “pods,” and they are divided by vertical columns of shelving called “bins.” A bin may have six to eight shelves, all tied together with mechanical linkage. That mechanical linkage is turned around on a steel track that is load bearing on the bottom and guide track on the top. Motors in the front and rear push and pull the product around on these tracks, guided by encoders and various electronic devices that ensure the bins stop at the right place at the right time. A light-directed device installed between the carousels can alert the operator to critical information, including the SKUs, quantities needed, and updated inventory counts.
Horizontal carousels are reliable and long-lasting
The internal mechanisms of horizontal carousels are durable and proven, and SencorpWhite has designed and installed thousands of them over the years. There are few, if any, consumable parts, so with the proper maintenance, these systems can last decades, or longer. We recommend quarterly check-ups by one of our factory-trained technicians. Or, alternatively, we offer training for in-house maintenance technicians. Preventative maintenance Includes cleaning and lubrication of wheels and chains, as well as an overall check to make sure all parts are in good working order. Regular scheduled maintenance helps ensure that the carousel will last without replacing any parts for decades of operation thousands and thousands of hours every year.
SencorpWhite offers several levels of service
SencorpWhite offers several different levels of service for horizontal carousels. For instance, we offer phone support as well as on demand service, where we respond to your call if you need help. We also offer maintenance contracts that include regular scheduled maintenance visits and/or can provide training for your operators and in-house technicians. Our goal is your satisfaction and our factory-trained technicians will work with you to make sure your horizontal carousel is operating at its best.
[Take it with you. Download the Guide to Understanding Horizontal Carousels]
Horizontal Carousel Variations and Special Features
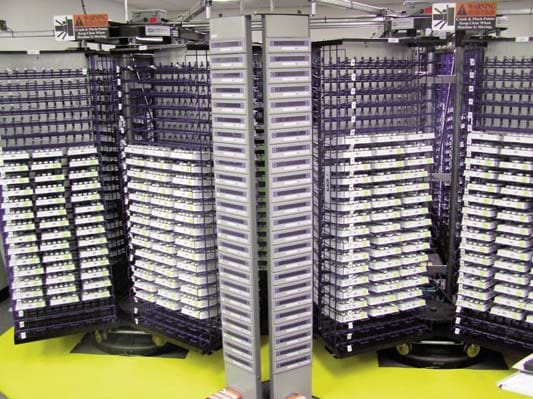
Horizontal carousels are versatile and they can be adapted to solve a variety of different storage and distribution challenges. For example, horizontal carousels can be stacked to maximize storage density within a small footprint. They are also routinely used in cold temperature warehouse environments and for the storage and distribution of heavy loads. Horizontal carousels can also be customized with special features such as fire suppression.
Horizontal carousels can be stacked to maximize storage density
For certain applications, two or three horizontal carousels can be stacked on top of each other. The compression weight holds the stack together, and operators can pick product off each mezzanine level, as items are conveyed up or down, either with a conveyor or a vertical reciprocating conveyor. Each horizontal carousel in the stack can rotate independently, clockwise or counter-clockwise, whichever direction is needed for optimum efficiency. Double- and triple-stacking horizontal carousels by themselves or in a pod can maximize picking efficiency while minimizing storage footprint. In certain instances, a storage robot, or “store bot,” can be added to pick items and then bring them either to a conveyance device or to an operator. These store bots can be particular useful for inhospitable warehouse environments (e.g., a meat packing plant where storage rooms are cold and dark) and/or where products are heavy or otherwise unsafe to pick.
Horizontal carousels can be used in cold temperature environments
Horizontal carousels are becoming increasingly common in the pharmaceutical and meat packing industries where products often need to be stored and picked refrigerated or frozen. Comprised of rugged, relatively simple mechanical components, horizontal carousels do not have many wear parts, making them ideal for various temperature environments.
Horizontal carousels can be built to move heavy loads
Horizontal carousels can be designed with a single piece of plate metal all the way around. Turned by big, heavy steel wheels, this plate can support heavy loads, including pallets of products, large automotive components, etc. This can be advantageous if a customer orders 29 skids of product and wants to come into the warehouse and inspect them before taking ownership. The skids can be picked onto the carousel, and the customer can walk around to check each one. After that, a fork truck can easily move the pallets from the carousel to shipping. Warehouses that take this approach have reduced fork truck traffic because the horizontal carousel can bring pallets of products directly to customers.
Fire suppression in automated storage solutions
Some automated storage applications require fire suppression features. Typically, these features involve water, but they can also involve chemical fire suppression or other specialized methods (e.g., altering the atmosphere in these enclosed environments with nitrogen or argon to remove oxygen). In vertical carousels, fire suppression systems are usually installed in the middle of all the shelves as they go up or in the top of the carousel itself. For VLMs, it is also common to put fire sprinkler and extinguishing systems in-between all the racks. For horizontal carousels, we typically run, in accordance with the customer’s requests, fire suppression systems between the faces of the carousels, so that there can be multiple tiers with multiple dispersion units. In grid systems, fire suppression usually involves saturation with water and can be quite complicated, depending on where in the cube the fire has started.
Horizontal carousels can be controlled manually or by computers
In certain situations, horizontal carousels can be controlled manually by operators using hand or foot switches that can move the carousel left or right, up or down. This type of manual control is suitable for lower pick rates in less complex warehouse environments. More commonly, however, horizontal carousels are controlled by computer software. Combining horizontal carousel hardware with warehouse management software means that orders can be controlled by a supervisor or an operations manager and then processed by operators using batch picking or single picking. In high order environments, computer-controlled horizontal carousels can enable picking at rates as high as 200 lines or more per hour. These accelerated rates are possible because the associated software is able to consolidate orders so that orders of the same items can be picked at the same time.
Horizontal carousels can help improve inventory management by integrating with legacy MRP and ERP systems
Combining horizontal carousels with warehouse management software enables replenishment and picking using whatever method works best for each business. For example, in some industries, date codes or freshness codes are a top priority, and inventory must be managed using a “first in, first out” approach. Alternatively, for other industries, a “last in, first out” approach is optimal. The software can be customized with rules appropriate for different business challenges, and it can be integrated with legacy MRP and ERP systems. At SencorpWhite, our goal is to provide solutions, not just equipment. We take a real systems approach and are able to design hardware and software to meet your business needs.
Optimizing slotting and batch picking to accelerate pick rates
Fast pick rates are possible when computerized warehouse management solutions optimize and integrate slotting and batch picking. Slotting is the term used to describe how items are physically stored. For maximum efficiency, the fastest moving items should be the most ergonomically accessible for picking—typically, that’s 42 to 46 inches high off the floor. Likewise, the slowest moving items should be stored in less accessible locations. Once slotting is optimized, batch picking becomes more efficient. With batch picking, the most items common to multiple orders are pulled together and arranged in a queue so that “batch” can be picked. Slotting and batch picking are optimized when horizontal carousel hardware and warehouse management software are integrated and customized for your business application.
[Take it with you. Download the Guide to Understanding Horizontal Carousels]
How To Determine What Type Of Horizontal Carousel Would Be Appropriate for Your Warehouse
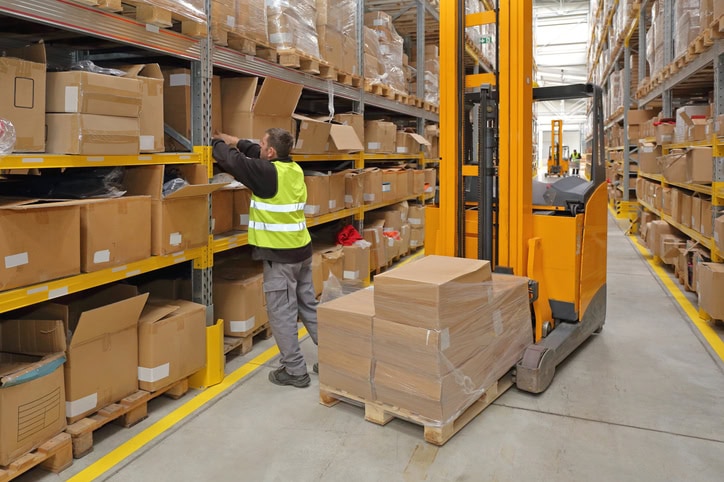
When we begin working with a customer, one of our first priorities is to analyze their database of products (size, weight, cubic footprint) and what their sales look like, down to kitting. We also analyze velocity reports by product, by SKU, and determine peak and average pick times. Then we ask, “Where would you like to see improvement? What issues are important to solve first?” We create solutions based on the answers to those questions. For example, a customer may have issues with printing out product labels or consolidation. The solution for downstream printing may be having consolidation completed in the carousel, in the accumulation conveyor, or in some other place. We sort through the options and design solutions that work best for the customer.
SencorpWhite also offers a range of automated storage solutions
Some customers think they need a horizontal carousel, but our analysis may show that another type of automated storage solution would work better. SencorpWhite offers a range of options, including vertical carousels and vertical lift modules (VLMs), which can be optimal in applications where storage density is more important than pick rate. At SencorpWhite, we are able to fit storage systems for each individual application. We want to offer the solution that’s going to get you the biggest ROI, whether that’s a horizontal carousel, a VLM, a robotic picking store bot, or just a software upgrade.
The installation process for automated storage solutions
Installation processes are as varied as the automated storage solutions themselves. We have installed vertical carousels in pharmacies in less than 12 hours. In these cases, we were able to prep the area and complete the installation overnight so that in the morning, we could run the carousel and train the operators. The installation of horizontal carousels can take longer—up to a week—depending on the length and size of the equipment. The same is true for VLMs. A single VLM can be installed in just a few days, but installation of a multi-column VLM can take up to two weeks, depending on its height. Shuttle systems can take a few weeks, as well, and grid systems, which are even more complex, can require months for installation. At SencorpWhite, we don’t believe in coming back and making right what we should’ve done right the first time. If it’s going to be done, we’re going to do it right the first time.
[Take it with you. Download the Guide to Understanding Horizontal Carousels]
Take it With You
Download the Guide in pdf format.