A Guide to Understanding Vertical Lift Modules
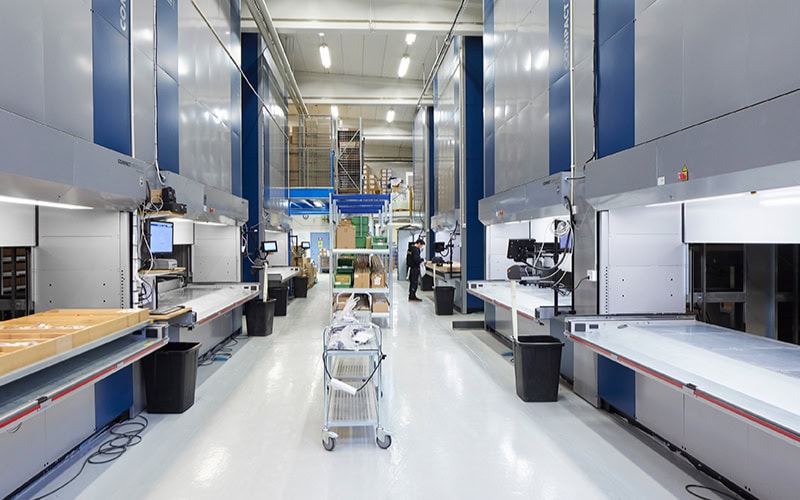
A Guide to Understanding Vertical Lift Modules explains how VLMs can provide automated storage solutions. These advantages include increased productivity, greater efficiency, and more effective use of space required. Identifying the system with features that best align with your company’s needs is essential.
This guide is divided into four sections. It will provide an overview of the features and benefits of using a vertical lift module storage solution.
How Vertical Lift Modules (VLMs) Are Used Across Industries
Competitive Advantages for Manufacturers using VLMs
See The Special Features Vertical Lift Modules (VLMs) Provide
Tips To A Successful Vertical Lift Module (VLM) Installation
How Vertical Lift Modules (VLMs) Are Used Across Industries
The key features that make them the optimal storage choice across a range of settings and industries.
A vertical lift module (VLM) is a storage solution that uses two stacks of trays. There is a centralized elevator in the middle of the forward and rear columns. This elevator runs vertically, retrieving trays and delivering them to the operator(s).
VLMs maximize floor-to-ceiling space, freeing up warehouse horizontal square footage for purposes other than storage. VLM shelving units are customizable for different product mixes. Multi-column systems can be designed to provide access for up to six operators which allows multiple users to use the same machine to retrieve the stored items.
The modular design makes them the optimal storage choice. This applies to many industries such as life sciences, aerospace, and e-commerce.
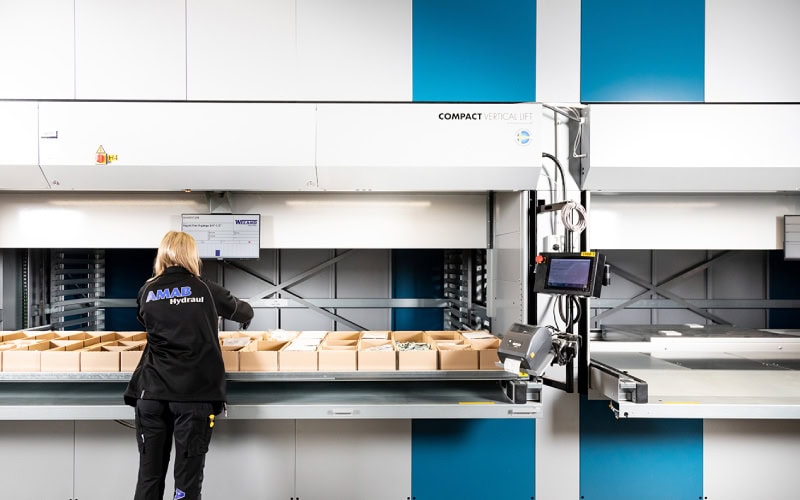
The key features that make them the optimal storage choice across a range of settings and industries.
A vertical lift module (VLM) is a storage solution that uses two stacks of trays. There is a centralized elevator in the middle of the forward and rear columns. This elevator runs vertically, retrieving trays and delivering them to the operator(s).
VLMs maximize floor-to-ceiling space, freeing up warehouse horizontal square footage for purposes other than storage. VLM shelving units are customizable for different product mixes. Multi-column systems can be designed to provide access for up to six operators which allows multiple users to use the same machine to retrieve the stored items.
The modular design makes them the optimal storage choice. This applies to many industries such as life sciences, aerospace, and e-commerce.
Why Vertical Lift Modules (VLMs) Can Provide Competitive Advantages for Manufacturers
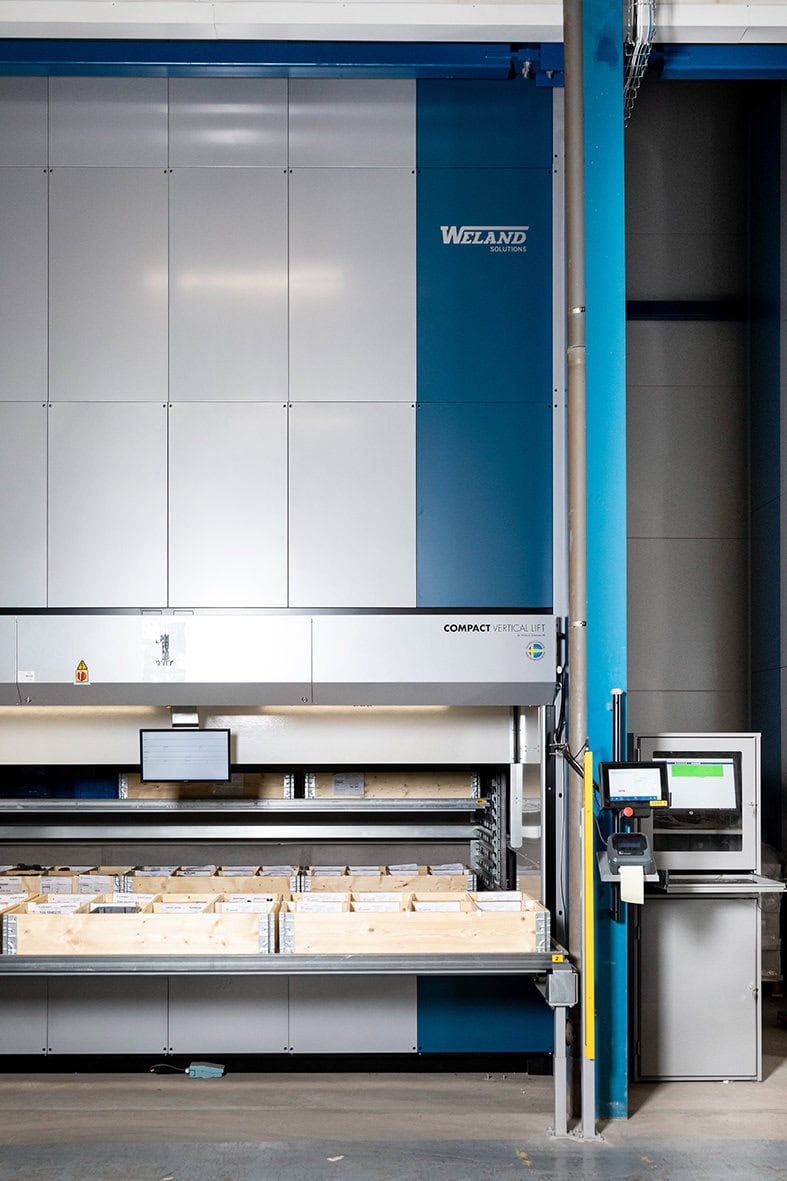
A popular storage choice across various warehouse settings and industries.
Vertical lift modules (VLMs) are enclosed and consist of vertical stacks of trays. These trays are connected by a centralized elevator that runs vertically between them.
The elevator can take commands and automatically collects and delivers the tray to the operator. This creates a goods-to-person pick solution.
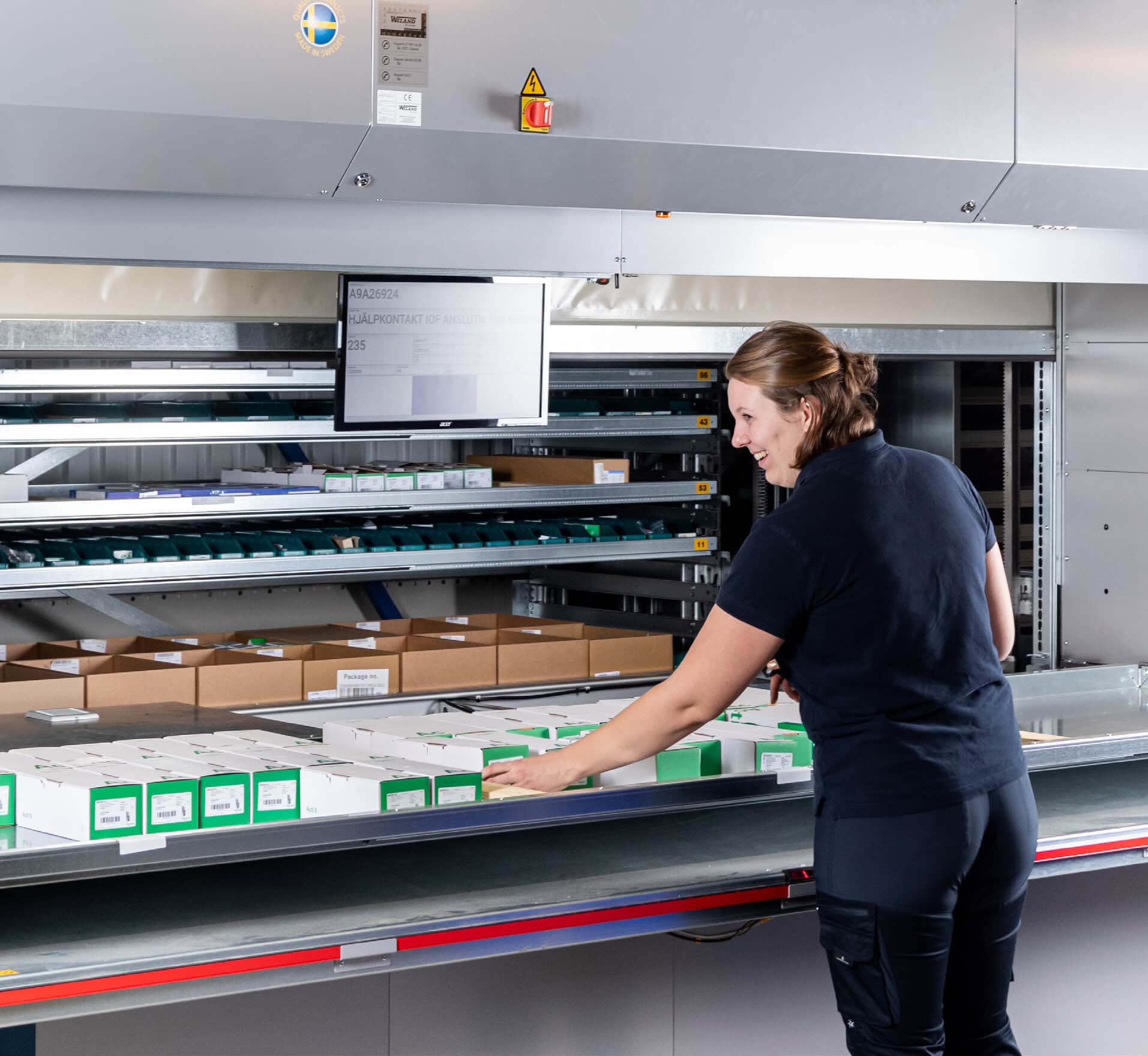
VLMs Increase Available Floor Space
VLMs have a small footprint, taking up limited floor space in the warehouse, which optimizes overhead air space and frees up floor space for other uses than storage. White Systems VLMs require up to 90% less floor space than conventional racking.
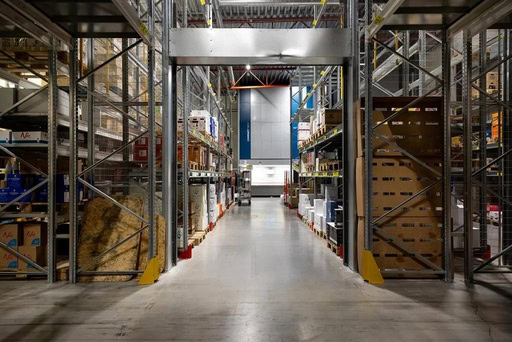
VLMs Accelerate Picking
The mechanical elevator runs between the tray stacks and automatically locates and retrieves specific trays as directed by the operator. At times, this can be completed in less than 45 seconds. Individual throughput rates will vary depending on the configurator and application. VLMs have a wide range of throughput capabilities of up to 500 LPH utilizing a pod of machines.
By offering customizable options for accommodating various product heights, VLM shelves optimize storage density, expand slotting choices, and enhance SKU management.
Multi-column systems can be designed to allow up to six operators to access at one time which reduces downtime and waiting periods.
VLMs Improve Picking Accuracy
VLMs are intelligent storage solutions with technology to improve picking accuracy, eliminate wasted operator effort, and increase customer satisfaction.
VLMs can incorporate pick-to-light systems employing light-directed technology for product identification or utilize verbal automation systems.

VLMs Provide Ergonomic Benefits
A VLM eliminates the need for an operator to bend and reach for items. VLMs present items at a consistent location so operators do not need to manually or use machinery to receive items. Ergonomic benefits like these enhance employee satisfaction and lead to improved warehouse productivity.
Unique Features of Vertical Lift Modules (VLMs)
Custom features for increased throughput, efficiency, and accuracy of the picking process.
VLMs enable companies to work more efficiently, speed up shipping processes, and maximize space utilization. This level of optimization is unprecedented.
The elevator is programmed to receive trays. It delivers them to an operator at a workstation. This improves throughput, efficiency, and accuracy.
VLMs can be customized with additional features to complement their basic functionality. These features include dynamic storage capabilities, multiple access openings, product identification systems, and specialized software integrations.
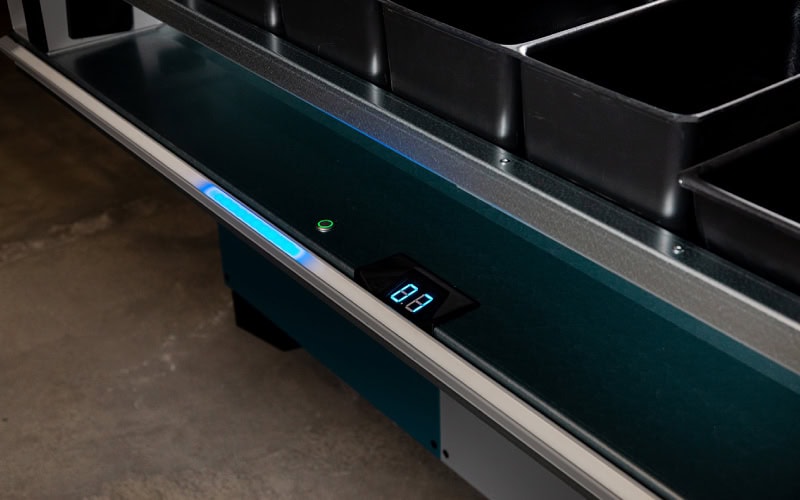
Dynamic Storage
VLMs are outfitted with modern hardware and software. This technology allows the shelves to adjust automatically to the size of the items being stored. This dynamic allocation of tray heights ensures maximum storage capacity with the VLM.
Dynamic storage makes VLMs ideal for companies storing parts or inventory that vary a lot in height.
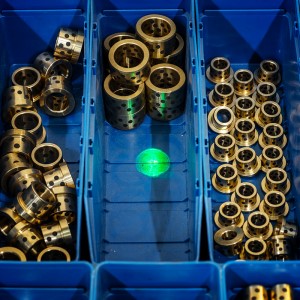
Multiple Access Openings
Multi-column VLMs can have up to six access openings, which allows multiple users to get products from the same machine simultaneously.
In other cases, access openings are located at the front and rear of the VLM. This allows items to be loaded and stored from one area and retrieved from another.
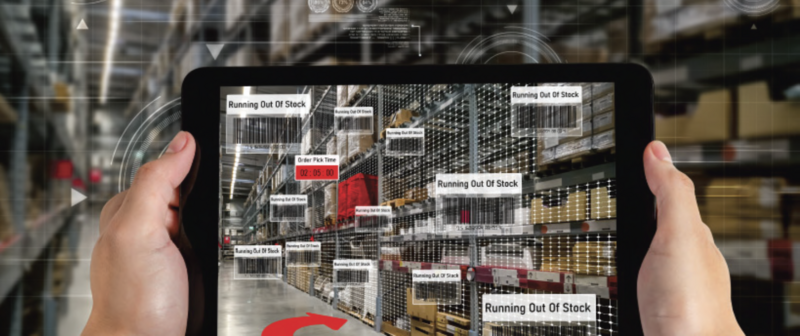
Specialized Software
VLMs are equipped with two types of software that must work together for optimal efficiency and productivity. First, the software is responsible for the overall functionality of the VLM, including dynamic storage capabilities and specific VLM options. In addition, VLMs use inventory management software that must be integrated with the host system.
Integration of inventory management can be accomplished in a variety of ways. A transaction processor can be implemented, allowing the host system to run the VLM and pull trays. Full-suite software can be run, enabling the host system and the VLM to maintain inventory. Running full-suite software creates duplicate inventory systems that can share information.
Inventory digitization is often a benefit of a VLM project. At White Systems, we have a wealth of experience integrating our vertical lift modules with WMS and ERP Systems for maximum efficiency.
Successful Vertical Lift Module (VLM) Installation
3 steps to consider while researching your options
Vertical lift modules (VLMs) increase productivity by helping companies use warehouse space more effectively and improve inventory management. Choosing the right VLM is essential to maximize the benefits. Consider your storage locations and business goals to select the best VLM.
As you research the various intelligent storage options now available, follow these three key steps
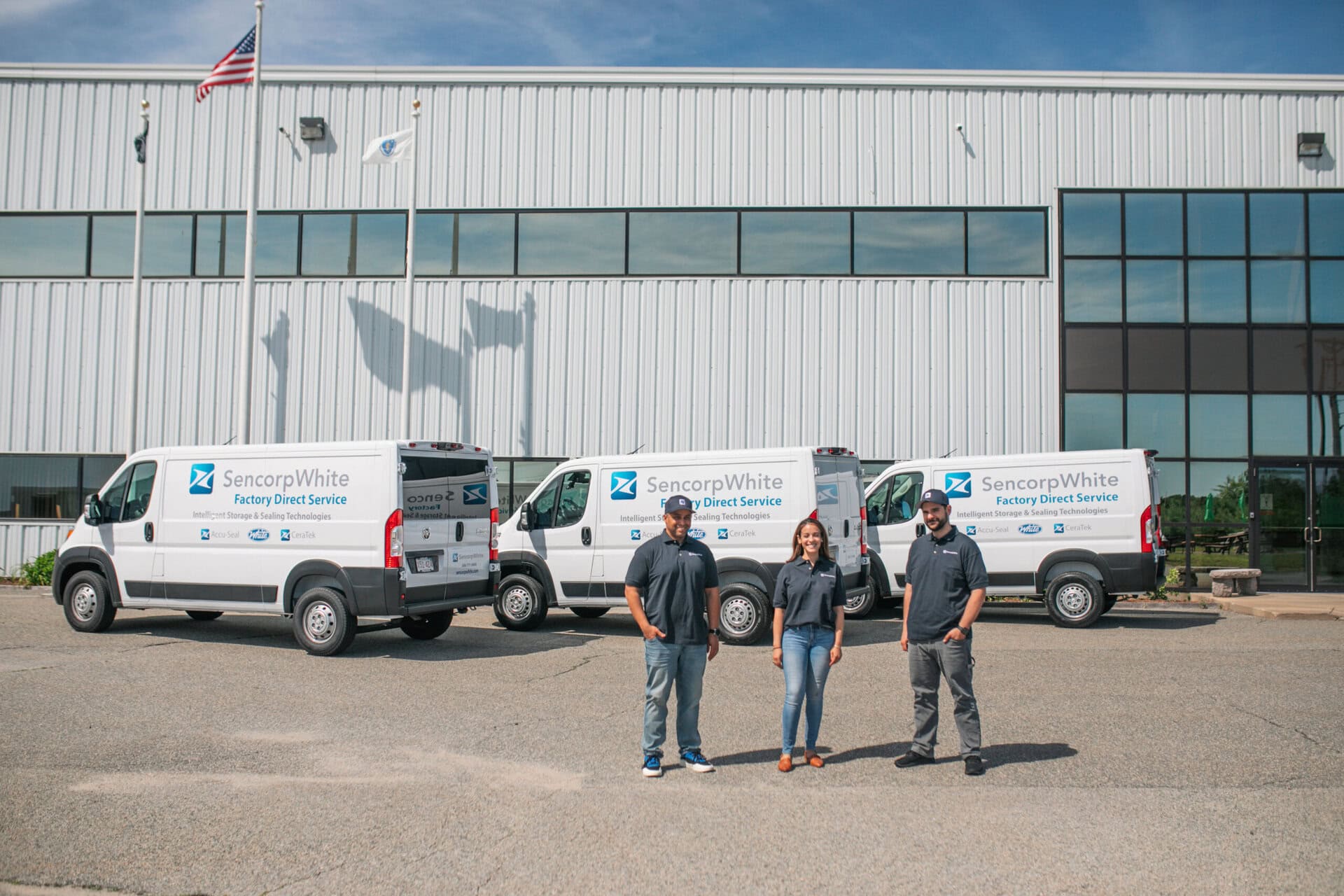
Step 1: Identify the problem you want to solve
The first step in selecting an automatic storage solution is to determine precisely what business issues you are trying to solve.
- Do you want to increase throughput?
- Does picking accuracy need to improve?
- Could you use more warehouse storage space?
Step 2: Determine available warehouse space, weight of products to be stored, etc.
VLMs are typically driven by site location and dimensions of the products needing storage. Because they are oriented vertically, VLMs optimize overhead air space and free up valuable floor space for purposes other than storage.
VLMs can also maximize storage density by automatically adjusting shelving based on the height of the items being stored. This dynamic allocation of tray heights makes VLMs ideal for companies storing parts or inventory that may vary in size.
Even so, it is also critical to consider the load rating of the shelving. Due to their size, they often have a low pound-per-square foot (psi) load rating. If you want to store smaller, heavy items, choose a multi-column VLM.
VLMs can be customized with a variety of different sophisticated features. Features offered are sophisticated product identifier systems, integrated inventory management software, and multiple operator access openings.
Required pick rates also play a role in selecting a VLM, a multicolumn VLM is the best choice because when speed is the priority, it maximizes throughput and minimizes operator wait time.
All our White Systems automated storage and retrieval units are fully customizable to meet each client’s unique needs. White has its factory-trained service technicians in field offices across the country. VLM service and scheduled maintenance needs will be completed quickly and reliably.
We take pride in our VLM hardware and software. We celebrate the superior customer service we provide before, during, and after the sale.
Take it With You
Download the Guide in pdf format.