Why Manual Inventory Management of Pharmaceuticals is a Thing of the Past
Pharmacies that do not utilize automated storage and retrieval systems face significant inefficiencies and challenges. Traditionally, pharmacies rely on horizontal shelving and manual processes to fulfill orders, leading to inefficient use of space and requiring staff to spend considerable time locating and organizing items.
Regulatory compliance, enforced by organizations such as the FDA and EMA, are crucial for pharmaceutical companies. Traditional inventory management practices often lack the traceability and record-keeping abilities necessary to meet compliance regulations. Without barcode tracking and robust security features, accuracy depends on manual counting and placement by staff, increasing the risk of picking errors and complicating documentation and quality control.
In the event of a recall or audit, productivity suffers as companies manually locate and account for specific product batches. However, by integrating vertical carousels pharmacies can significantly improve their operational efficiency and productivity.
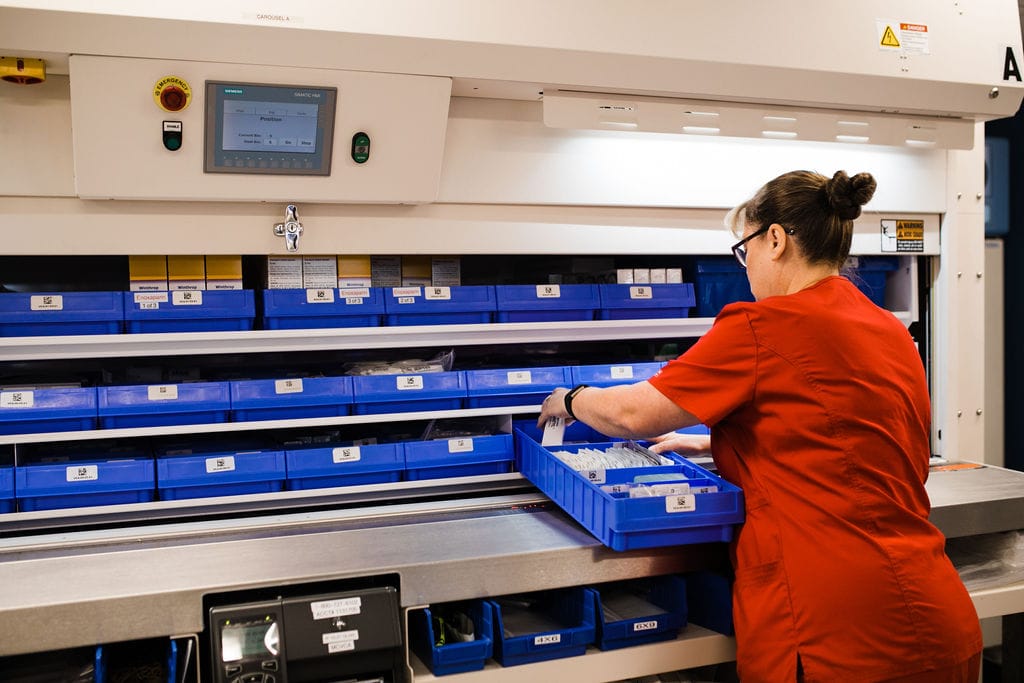
From Manual to Modern: How Automated Pharmacy Storage Systems Are Changing the Game
Where traditional methods are lacking, automated systems excel. Automated pharmacy storage systems are revolutionizing inventory management with advanced technologies and efficient methodologies.
- Vertical lift modules: Automatically store and retrieve trays with goods for more accurate picking.
- Vertical carousels: Streamline inventory management, reduce storage footprints, and enhance workflow and productivity.
- RFID technology: Provides real-time inventory tracking, ensuring pharmacies maintain optimal stock levels and reduce wastage.
- Robotic dispensing systems: Streamline operations in high-volume settings, reducing labor costs and minimizing dispensing errors.
- Automated Dispensing Cabinets (ADCs): Enhance medication safety at the point of care.
Choosing the right technology can be a pivotal investment for your company. One of the leading technologies in the industry for inventory management are vertical carousels.
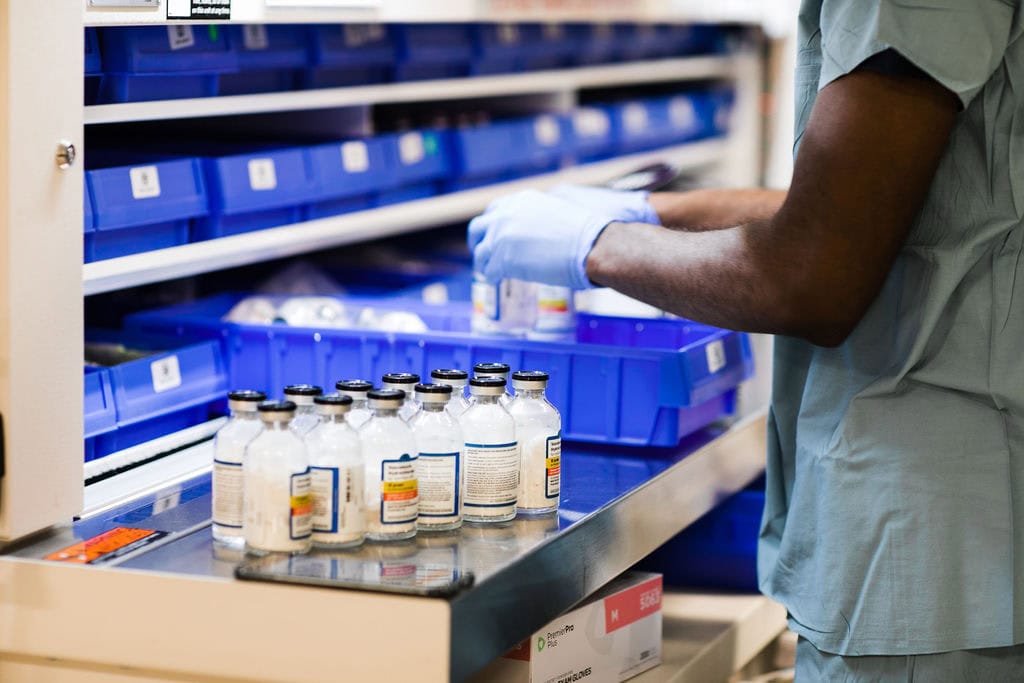
How Vertical Carousels Transform Pharmaceutical Inventory Management
Embracing the cutting-edge technology of vertical carousels paves the way for transformative improvements in inventory management, ensuring your business is future-proof and scalable.
Synchronized with frequency identification technology (RFID), automated dispensing systems, and warehouse management interfaces, vertical carousels are equipped to significantly improve inventory management for pharmaceutical companies. In simple terms, the carousels use vertical shelving units that move up and down. Computerized control systems locate the requested item and rotate the carousel to bring the desired tray or shelf to the retrieval position, making it easy and accurate for the operator to access the item.
Automated pharmacy storage systems notably enhance operational efficiency and accuracy. With barcode infographics assigned to each product, the system’s comprehensive tracking and documentation capabilities provide clear visibility into inventory levels, enabling better decision-making. This integration ensures all aspects of inventory management align with regulatory requirements, further enhancing compliance. Automation reduces human error, ensuring the correct product is in the right place. Precise inventory tracking capabilities also monitor expiration dates and simplify locating recalled products. With the ability to operate 24/7, the systems help to reduce lead times, labor costs, and improve overall productivity.
Space utilization is another key benefit of vertical carousels. They maximize underutilized vertical space in factories and warehouses, increasing available floor space and storage density. Centralizing the storage of pharmaceutical products streamlines inventory management and enhances operational workflow. This reduces the storage footprint and frees up valuable floor space for other critical activities such as packaging and processing. Pharmaceutical companies can then expand operations within existing premises without costly expansions or relocations. Efficient use of vertical space optimizes the physical layout and significantly impacts overall operational efficiency and scalability.
Vertical Carousel Features Streamline Efficiency and Productivity
With a multitude of features tailored to meet your specific needs, our solutions are designed for versatility and efficiency. We offer various sizing options and optional refrigeration to cater to customizable storage requirements. Here are some of the key features:
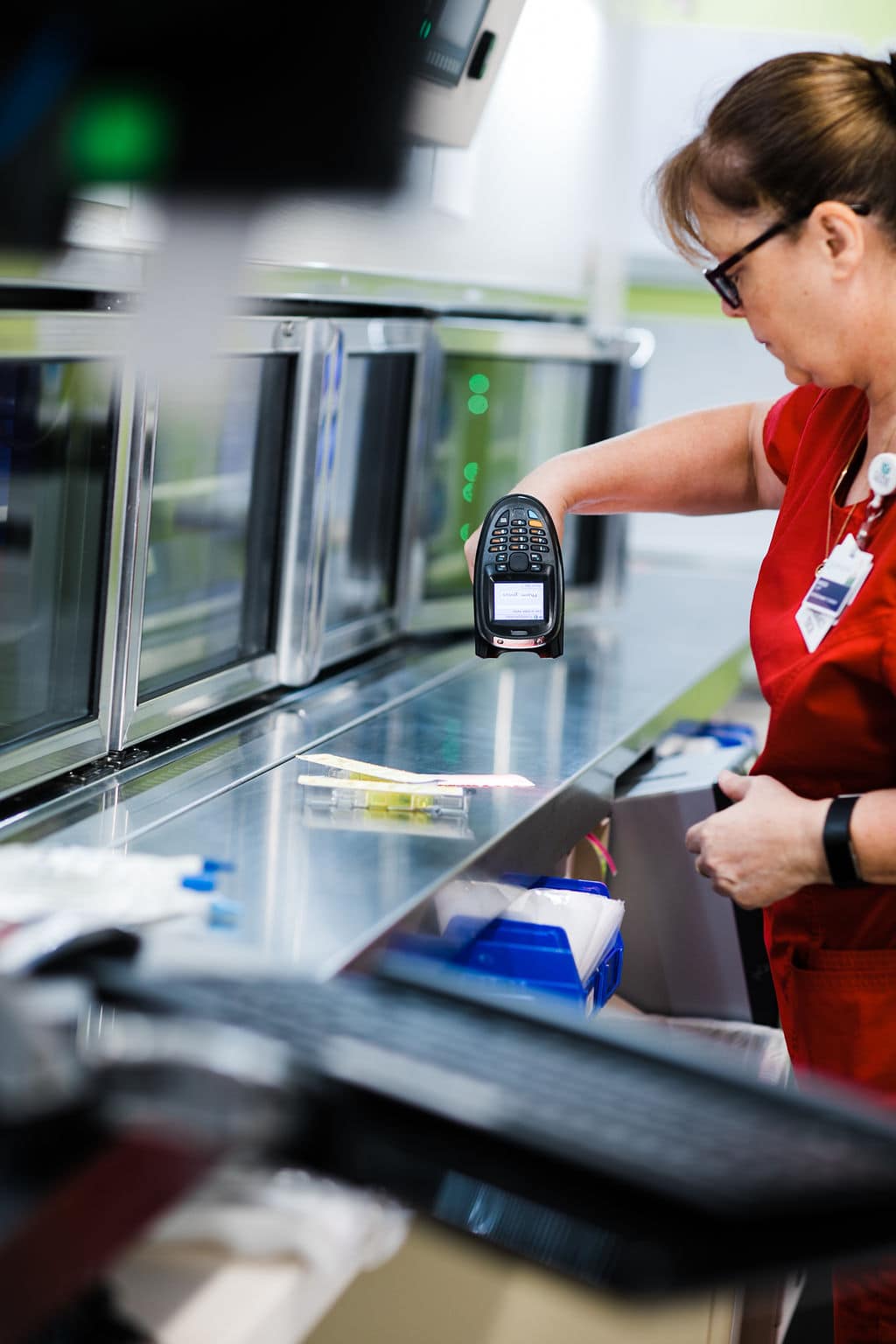
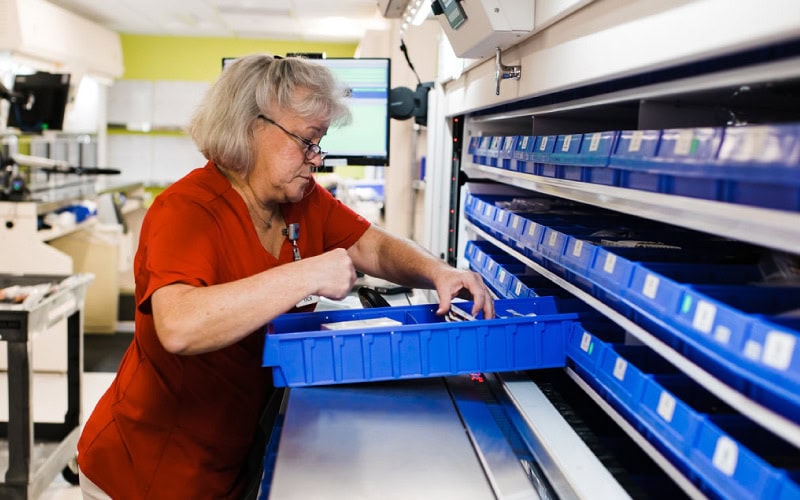
- Pick-to-Light Feature: Lights up on the counter to identify the product, the quantity needed, and the part, serial, or stock number.
- Radiofrequency ID (RFID) Tags: Placed on each product inside the vertical carousel to verify and track inventory, product expiration dates, and other processes.
- Ergonomic Height: Vertical carousel delivers items to technicians on a tray table 40 inches from the ground, reducing injury and increasing productivity.
- Interface with WMS, WES, and ERP Systems: Allows for synchronization of warehouse management.
- Optional Totes, Bins, and Drawers: Efficiently organizes inventory.
- Optional Refrigeration: Ensures medications retain their therapeutic effectiveness and composition. (Highly Recommended)
A Real-World Application: How Vertical Carousels are Transforming Pharmaceutical Inventory Management
Hospital pharmacies, averaging 2,000 square feet, need to simultaneously store medications and provide workspace for pharmacists and technicians. With the ability to reduce storage footprints in hospital pharmacies by at least 50% by replacing static shelving with vertical carousels, White Intelligent Storage has been proven to adequately improve spacing optimization. For example, a pharmaceutical company required 28 fridges across multiple hospital locations to properly store products. With vertical carousels integrated, the company centralized refrigerated storage to a single location, enhancing efficiency and accessibility.
Transitioning from manually sorting inventory, which could take up to four hours for a 24-hour supply, to an automated system has enabled technicians to fill and replenish orders efficiently and productively. Advanced tracking capabilities through barcode scanning have significantly decreased the risk of human error, ensuring that the correct products are consistently delivered to the right locations. This enhancement has halved production time, allowing technicians to engage in more specialized tasks. Implementing vertical carousels not only optimizes space but also boosts efficiency and productivity for pharmaceutical companies.
Conclusion
Replacing manual inventory management practices with automated pharmacy storage systems is essential for optimizing space, enhancing operational efficiency, and boosting productivity. Embracing this technology is not just an upgrade—it is a necessary step forward for pharmacies aiming to thrive in an increasingly complex healthcare environment.
For those looking to elevate their pharmacy’s inventory management and operational efficiency, exploring vertical carousels could be transformative. Consider reaching out to our sales team for personalized recommendations and more detailed information on how our solutions can meet your specific needs.