Horizontal Carousels Transform a Three-Day Warehouse Backlog into Same Day Shipping
Horizontal Carousels Transform a Three-Day Warehouse Backlog into Same Day Shipping
Challenge
Challenge
In Columbus, Georgia a life insurance company faced the obstacle of downsizing their literature distribution facility from 60,000 sq. ft. to 10,000 sq. ft.. This significant reduction in storage space left the company seeking out more efficient storage solutions. With the distribution of thousands of different forms, booklets, calendars, and promotional premiums to over 14,000 associates in 4 states, the company also wanted a system that would provide same-day shipping and increased picking rates.
Solution
Solution
After analysis of the company’s available space, a White representative recommended a horizontal carousel system because it offers attributes of speed and organization that makes it ideal for firms distributing large volumes of different types of printed forms. Each carousel was equipped with 70 bins, 24 1/2 inches wide and 16 inches deep.
There were eight shelves per bin with each shelf holding two boxes of forms in the original shipping carton, totaling to a capacity of 5600 items. With clear visibility into a queued list of up to 250 item’s locations, picking speeds were automated and accelerated to precisely meet demands.
The system uses a “pick and pass” concept. The carousels are set up in two zones, each with its own operator. At the first zone, the operator selects the items located in the zone’s three carousels. As the operator picks from one carousel, another is moving, brining bins with the next items to be picked to the operator. Waiting time is virtually eliminated.
The tote with the partially completed order is then passed to the second zone, where the operator picks the rest of the order from the zone’s two carousels. The completed tot is pushed onto a conveyor to packing and shipping.
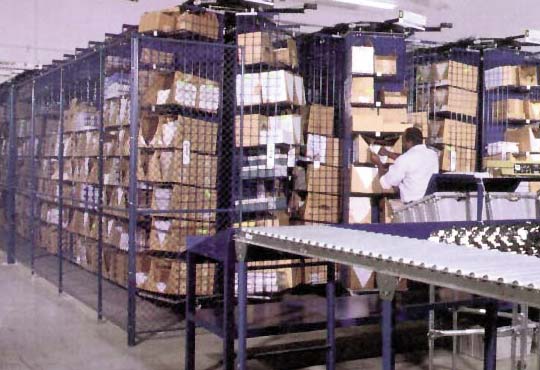
Piking speed is further increased because the operator doesn’t have to count. Most items are shrink-wrapped in standard quantities and can only be ordered that way. Other items are weighed to determine quantity. Two packers, nearby, pack the items and affix the shipping labels. The system produces and an order, ready to go, approximately every three minutes.
Each morning, before the picking routine begins, the carousels are restocked. This takes about an hour. The inventories are taken from a storeroom that holds bulk quantities received from forms printers and similar sources. Picking is performed for a full eight hours. The engineering staff at White tailored the system’s design to complete the building’s configuration
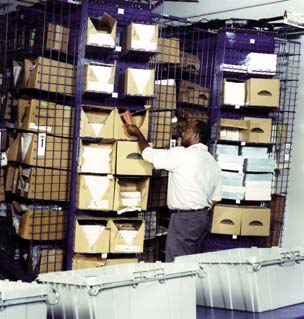
Results
Results
The company decided to have 5 White horizontal carousels installed to alleviate their current challenges. With manpower being reduced by as much as two-thirds and operator productivity increased by 300%-400%, the company saw a quick return on their investment. Before the White carousels were installed, the company had been picking about 3000 lines per week using six people. Now, only two people are needed to pick 5000 lines. “We went from a three-day backlog to same-day shipping,” says the manager of supply services. Since the move to the smaller facility had to be made without reducing inventory, choosing the proper equipment was a necessity. In fact, the inventory has since increased from 3300 items stocked to nearly 4000.
The carousels extend from beneath an office mezzanine and were built around several building columns to maximize floor space utilization. The company’s potential future needs were also considered.
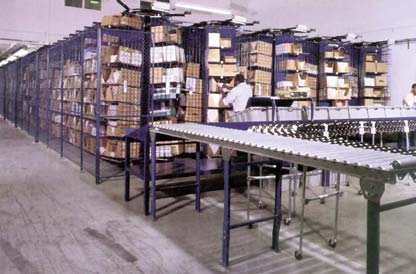
Eventually, the system would be entirely computer controlled with order and item location information fed directly into the carousel system. This should further increase picking speed and accuracy. More carousel units can be added to the system to expand its capacity and shelving arrangements can be easily modified.
Since the White carousels were installed, the room which houses them has become a “must see” for visiting associates touring their facilities. “The system is fool proof,” observes the manager of supply services. “We haven’t had a day of downtime.” However, she added that the bottom line “is the service it has allowed us to provide our associates across the country.”