The mechanism that drives a vertical carousel is similar to the mechanism that drives a Ferris wheel.
However, rather than rotating on a circular path, as a Ferris wheel would, the shelving units move up and down vertically, following an elongated oval path. The rotation is driven by a motor that spins a drive chain, which is attached to a torque tube extending across the interior of the carousel.
This creates what is called a “drive side” and an “idle side.” But because the torque tube on the drive shaft is synced with the drive side, when the drive side spins, the idle side spins, generating the vertical motion up and around, over and over.
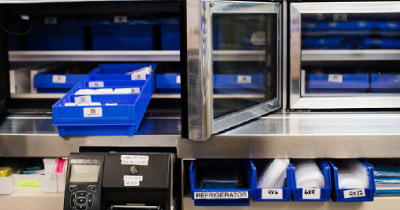
Once that signal is received, the motor spins the drive chain attached to the torque tube, and the vertical carousel turns to present the right shelf at the counter. At the same time, the pick-to-light feature on the counter identifies the product to be picked, the quantity needed, and the part, serial, or stock number. The operator can then pick the product and scan its bar code, verifying that they are picking the right product and the right quantity at the right time.
Safety is top priority
Years ago, the industry standard for vertical carousel safety was a light beam emitted from one side and received by a reflector on the other side (similar to how a garage door sensor works). However, today’s safety features for vertical carousels are much more advanced. White vertical carousels have a primary logistics controller (PLC) that continually checks the system to verify that every movement is safe. We utilize a light bar that scans the entire opening width from top to bottom and back and forth. If there is ever a break in that invisible plane of light, the machine comes to an immediate halt, preventing damage to person or product.
In addition to PLCs, White vertical carousels are equipped with overload and obstruction sensors. If there is too much weight, either vertically or horizontally, sensors recognize the overload and stop the vertical carousel from moving. Similarly, if product becomes loose or breaks off somewhere, sensors can recognize the obstruction, apply the brakes, and bring the machine comes to an immediate halt.
White vertical carousels are durable and reliable
White vertical carousels are built to last. For example, the New Orleans Hall of Records is still operating machines that we built in 1974. The key to this kind of longevity is preventative maintenance. Just as with a car or house, a vertical carousel will function best if it undergoes regular maintenance and occasional mechanical refreshes. White is the only vertical carousel manufacturer in North America with a dedicated in-house team of Field Service Engineers. This factory-trained service team is conveniently located throughout North America and provides the highest quality service available in the industry.