Largest Mail-Order and Online Seed Company Improves Warehouse Efficiencies With Horizontal Carousels
Largest Mail-Order and Online Seed Company Improves Warehouse Efficiencies With Horizontal Carousels
Challenge
Challenge
The largest family owned mail-order and online seed company in the world was looking for an inventory management solution that would streamline its productions. “To continue our market leadership, we realized the need to use new technologies to provide our customers with the fastest and most accurate service possible,” said the VP of Information Services. With the vast majority of sales for the company occurring from December to April, the company receives thousands of orders within this 16-18 week period.
For over 20 years, the company relied on a manual filling system. With large wooden bins outlining the perimeter of the filling area, up to 50 fillers would be hired to fill the orders in two similar areas. Single orders would be printed up and a filler would circle the perimeter picking in numerical sequence. Every order had to be checked for accuracy. Up to 20 checkers had the responsibility of checking all orders going to the packers.
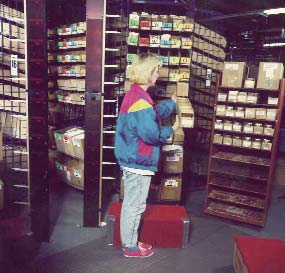
Solution
Solution
To fill the vast majority of the company’s orders, three pods of four horizontal carousels with 26 bins each were installed. Each pod was equipped to fill 16 orders simultaneously utilizing Lightree displays and sort bars.
Pod one splits time storing seed, retail bulbs, and small perennials depending on the season. The shelves within the bins and the Lightree display are simply readjusted to accommodate the different sized inventory. Pod two is strictly used for seed filling. Over 2000 varieties of plants consisting of 5000-6000 SKUs reside in the pod. Popular items have multiple positions within the carousels to speed picking and increase storage capacity.
Pod three is strictly to fill seed orders during peak season. It also serves as a training system during off peak. All three pods are linked via conveyor to the packing area. When an order is received it is first validated in the mail room. Then it enters the editing area where the orders are checked to determine if all needed information was filled out. If so, the order is keyed-in and the information interacts with current inventory.
The order is then received and released via a software link to the carousel filling area. The license plate on a tote is scanned to link that tote and a specific order within the computer.
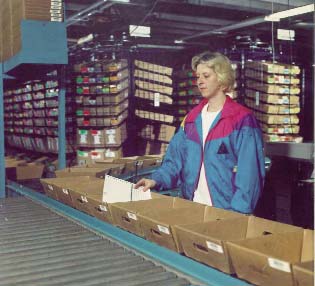
The order is batched and downloaded to activate the lightree displays, sort bars and carousels. Once all 16 orders are completed, the tote is pushed from the sort bar area to a conveyor right behind it. The conveyor takes the order to the packing slip area. The license plate on the tote provides the computer with the proper identification and the correct packing slip is printed and place with the order.
The tote then proceeds down the conveyor to the packaging area where it is packed and shipped. Replenishing the inventory on the carousels occurs between waves of orders. Replenishing is completed between waves of orders by the picker.
Results
Results
After integrating the carousels, orders were filled within 24-36 hours. Even at 950-1000 lines picked per hour, per pod, the carousels were able to be ran 24 hours a day to meet the flow. The company saw their pick rate go from 180 to over 950 lines per hour, per picker. They entrusted a significant portion of their business to White’s horizontal carousels and experienced the results listed below:
System speed when compared to the prior system, jumped from 180 to 950- 1000 lines per picker per hour with orders being filled within 24-36 hours.
Space Savings allowed an entire storage area to be drastically reduced and the recovered space utilized for other purposes. This is attributable to the carousels’ effective use of vertical cube. After seeds are packaged they are placed directly on the carousel not in a stock room.
Reduces manhours to less than 1/3 of what had been required prior to the carousels. During peak season nine fillers (pickers) are now used instead of 50 and three checkers instead of 20.
Reduced error rate can be attributed to two factors…equipment and personnel. The use of the LightreeTM displays, indicating position and quantity of the pick, minimizes human error. “Staffing is improved,” said Earline Lindley, order processing assistant manage “needing only several fast and accurate fillers allows us to be very selective.”
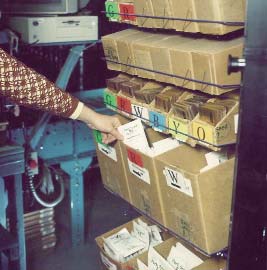
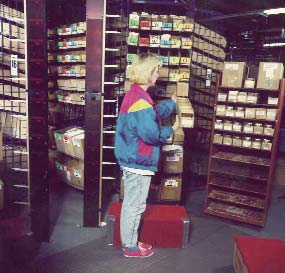
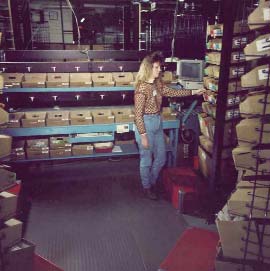