To overcome the challenges associated with the click and collect business model, grocery retailers can choose from a variety of storage solutions, each with their own distinct advantages and disadvantages.
These options run the gamut from traditional shelving and storage lockers located within existing stores all the way to separate micro-fulfillment centers equipped with automated intelligent vertical storage.
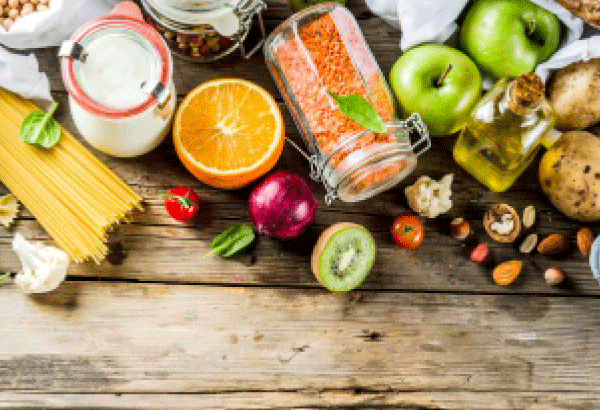
Storage lockers
Storage lockers are a relatively inexpensive solution for product storage and retrieval, and they have been used successfully in standard retail. Unfortunately, though, these systems have significant downsides for grocery eCommerce. For example, most storage lockers do not offer temperature regulation, limiting their application for orders needing refrigeration or freezing. Storage lockers can also be problematic when there is high product turnover. That’s because the density, or storage capacity, of storage lockers is low. When there’s only one space for product to go in, and one space for product to go out, replenishing and restocking becomes a big headache, especially in large pickup environments.
Another disadvantage to storage lockers is that they must remain at fixed locations easily accessible by humans. That means that if a grocer wants to expand their footprint of locker-based solutions to handle more orders, they have no choice but to expand horizontally. Most grocery retailers don’t have the real estate or floor square footage to accommodate the storage locker solutions needed to meet increased customer demand.
Automated intelligent vertical storage
Many grocery retailers are evolving beyond storage lockers to automated vertical storage solutions. These free-standing storage and retrieval carousels can be installed within a store, in a parking lot, or on the exterior of a wall to create additional store square footage. They provide high intensity storage for enhanced throughput, ergonomic loading and pick up, scalability, and in some cases, temperature-controlled environments. In short, automated intelligent vertical storage solutions are able to improve order fulfillment speed and accuracy, while reducing costs and preserving margins.
Grocers wanting to implement automated vertical storage solutions can choose between two options: shelf-based systems (also called vertical carousels) and vertical lift modules.
In a shelf-based system, the shelves rotate around in an oval pattern and they are loaded with totes. The totes contain the grocery orders for customers, and they’re stored until customers are ready for pickup. Because it utilizes vertical space, a shelf-based system is an efficient way to store large quantities of orders, and the orders can be easily queued up when a customer arrives for pick up. In addition, vertical carousels are reliable and simple for operators to learn and use.
A vertical lift module is more complex. In a vertical lift module, a robotic platform actually retrieves whatever is being stored in the compartments within the vertical unit. Like vertical carousels, these systems optimize vertical space, but because of the robotic integration they can be pricey.
Vertical carousels and vertical lift modules also differ in their manual de-stage processes. For example, the White vertical grocery carousel has mechanical retrieval that can be run by the operator if the unit does go down for some reason and orders need to be retrieved. By contrast, if the elevator inside a vertical lift module goes down, the orders must continue to be stored until the technology can be fixed.
Shuttle-based systems within micro-fulfillment centers
Several large grocery retailers are now opting for shuttle-based systems as a storage and retrieval tool within large micro-fulfillment centers. These are grid-based block systems, where the blocks are stacked on top of each other. Small robots search for and relocate those blocks, bringing them to stations where orders can be picked and filled. These systems can efficiently handle a large number of SKUs; however, they do require a significant amount of floor space—and a considerable investment.