Custom features for increased throughput, efficiency, and accuracy of the picking process.
Today’s Vertical Lift Modules (VLMs) are intelligent and versatile, enabling companies to work smarter, ship faster, and use space more effectively than ever before.
Comprised of stacks of shelves with a centralized elevator running between them, VLMs function as true goods-to-person delivery systems. The elevator is programmed to retrieve certain trays and present them to an operator at a workstation, increasing throughput, efficiency, and accuracy of the picking process.
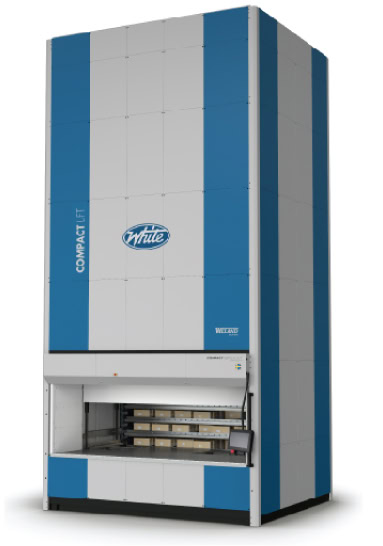
To complement their basic functionality, VLMs can be customized with additional features, including dynamic storage capabilities, multiple access openings, product identification systems, and specialized software integrations.
Dynamic Storage
VLMs are equipped with innovative hardware and software that can automatically adjust shelving based on the height of the items being stored. This dynamic allocation of tray heights ensures maximum storage capacity with the VLM.
Dynamic storage makes VLMs ideal for companies storing parts or inventory that vary a lot in height, and it is one of the primary reasons these units have become so popular.
Multiple Access Openings
Multi-column VLMs can be designed with up to six access openings. These access openings are often located next to one another other, so that multiple users can retrieve product from the same machine at the same time, with minimal downtime and waiting. In other cases, access openings may be located at the front and rear of the VLM, so that items can be loaded and stored from one area and the retrieved from another.
As an example of what’s possible with multiple access openings, one of our customers in the life sciences industry needed a VLM that provided operator access from both a clean room and a warehouse. We customized a solution that allowed product to be loaded from the clean room side, and then shipped from the warehouse side.
IRIDE System
White’s ICAM VLMs includes the IRIDE system, which displays not only order information, but also exactly what part the operator needs to pick from the tray. This increases the accuracy and speed by better informing the operator. Other VLMs have simpler product identification systems, such as pick-to-light systems that use light-directed technology to identify product locations or voice automation systems that use verbal commands to drive the operator to a specific cell. Often these systems employ a double check process slowing down pick rates.
Systems that precisely identify items for picking, like IRIDE, improve throughput and order accuracy, leading to greater customer—and operator—satisfaction.
Specialized Software
VLMs are equipped with two types of software that must work together for optimal efficiency and productivity. First, there is the software responsible for the overall functionality of the VLM itself. This software runs the machine, including dynamic storage capabilities and certain VLM options. In addition, VLMs use inventory management software that must be integrated with the host system.
The integration of the inventory management can be accomplished in a variety of ways. For instance, a transaction processor can be implemented, allowing the host system to run the VLM and pull the needed trays. Alternatively, full suite software can be run, enabling both the host system and the VLM to maintain inventory. Running full suite software creates duplicate inventory systems that can share information and keep records up-to-date.
Inventory management software can be the driving force of a VLM project, and at SencorpWhite, we are fortunate to have both Intek and Minerva, two software companies with expertise in this area.