Selecting the most suitable automated storage and retrieval system (AS/RS) for your warehouse, distribution center, or manufacturing facility can be challenging. Vertical Lift Modules (VLMs) can increase the throughput, efficiency, and accuracy of the picking process.
In this guide, you’ll find everything you need to know to get started with VLMs, including:
- What a VLM is and how it differs from other storage solutions
- The different types of VLMs and how they work
- The VLMs that offer the fastest throughput and the most storage density
- The most common VLM options
- Features to review when evaluating a VLM
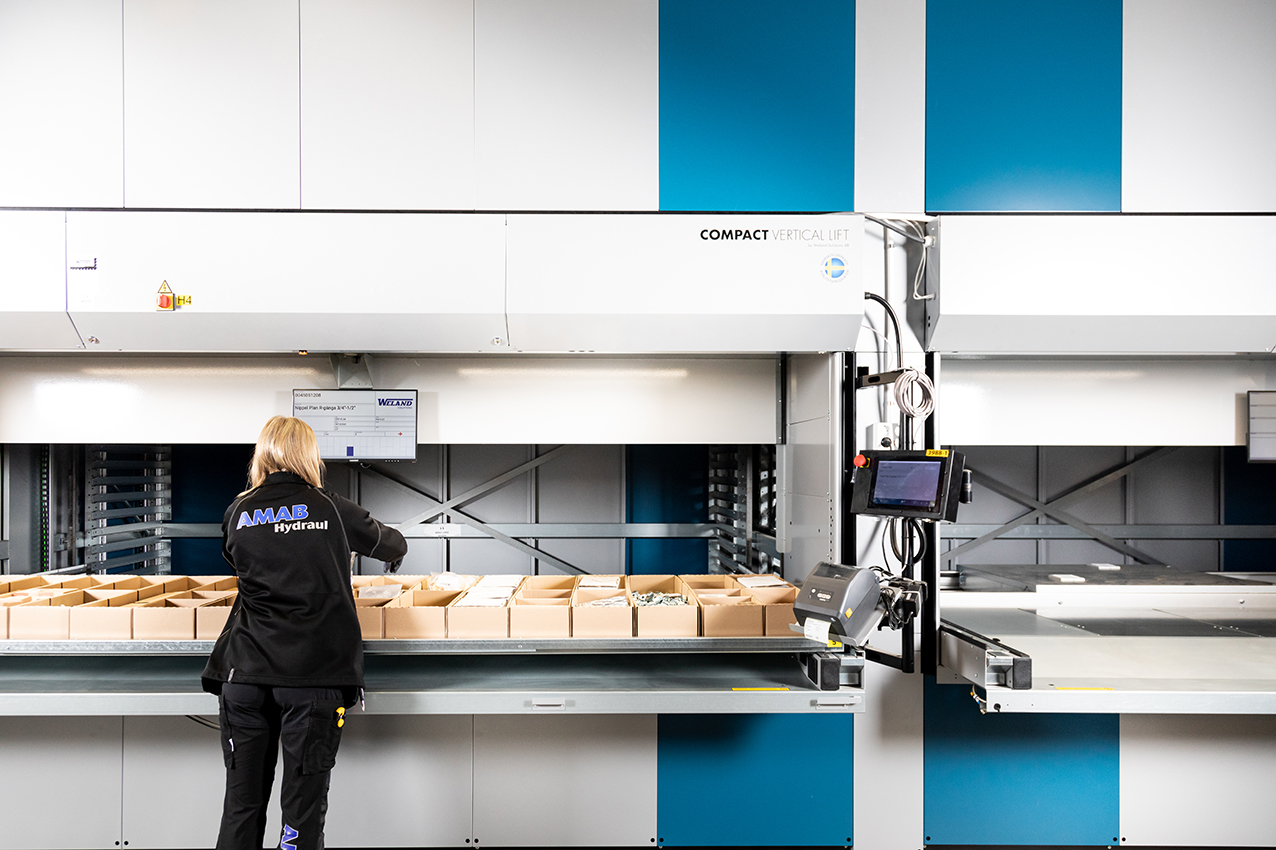
What is a Vertical Lift Module (VLM)?
A vertical lift module (VLM) is an enclosed automated storage and retrieval system (AS/RS) known for increasing productivity. It consists of two racks of shelves stacked upright with an elevator or extractor running vertically between them. The elevator responds to commands and automatically retrieves and delivers trays to an operator at a workstation.
VLMs are often used in warehouses, distribution centers, and factories to improve picking speed, enhance space savings, efficiency, and accuracy.
How a Vertical Lift Module (VLM) is different than a vertical carousel
A vertical carousel has shelves that rotate vertically on a fixed elongated oval path. The shelves are driven by a mechanism that is similar to the mechanism that runs a Ferris wheel. By contrast, with a VLM, only the desired tray is extracted and moved.
A VLM and a vertical carousel differ in their movement. In a vertical carousel, everything moves, while in a VLM, only one tray moves at a time. Weight capacity is typically higher in VLMs. The trays in the vertical carousel have a fixed distance between them and is ideal for storing fixed height material or totes. VLMs are ideal for storing items with different heights.
The different types of Vertical Lift Modules
Vertical lift modules (VLMs) have evolved considerably, and now they have a wide range of capabilities, specifications, and features.
Compact Lift: Single column, single elevator VLM
The single column, single elevator VLM has historically been the most common VLM. It has two racks of shelves stacked vertically with an elevator or extractor system running between them. The elevator extracts one tray at a time and delivers it to an operator at their workstation.
Compact Twin: Single column, dual elevator VLM
A single column, dual elevator VLM has two sets of shelves stacked vertically, with an elevator running between them. However, with the single column, dual elevator VLM, the extractor is capable of holding two trays at the same time. The extractor can pick up one tray and give it to the operator. While the operator is picking, the elevator can return the previous tray and pick up the next one. So, it is working while the operator is picking and increasing operator pick speed. It is also very ergonomic as the tray is presented at the same height each time.
The double deep, dual elevator VLM is similar to the single elevator VLM. However, it uses two sets of trays in the front of the elevator and two sets in the back. It has the unique ability to retrieve a tray from a shelf that is located behind another tray.
This VLM machine provides the highest levels of storage density and can be valuable for a business to optimize floor space.
Multi-column, single elevator VLM
A multi-column VLM uses an extractor that moves both vertically and horizontally. A multi-column VLM machine can be useful for businesses to store and retrieve parts or products of varying heights and small but heavy loads. Pick speeds are slower due to the longer travel time required for retrieval with this system.
Single column, high speed tote based VLM
A single column, high speed, tote based VLM has an extractor with multiple picking totes. The machine has the ability to elevate and move totes. It can lift one tote to the side, then lift another container. Finally, it can move the second tote to the opposite direction.
This method enables the operator to receive all five different picks simultaneously instead of one by one. The operator can have all the picks they need for an order at once. The high speed VLM machine can accelerate throughput.
Pallet based VLM
A pallet based VLM is a VLM that can handle full pallets weighing up to 3,000 pounds. This is extremely useful when picking is done from pallets by the operator and entire pallets can be stored and retrieved for increased flexibility. Storing or induction of goods is easier as entire pallets can be loaded into the VLM rather than having to break down pallets to store on individual trays. Ideally, the VLM incorporates a separate structure to load and retrieve pallets into the VLM for added robustness for fork truck delivery.
How does a Vertical Lift Module work?
A VLM has an elevator that runs vertically between two stacks of shelves, one in the front and one in the back. The elevator can respond to commands and it automatically retrieves and delivers trays to an operator as instructed. Typically, the trays are delivered to a workstation at waist-high level (i.e., at the ergonomic “golden zone” of 37-40” high).
The Vertical Lift Modules that offer fast ergonomic throughput
When it comes to throughput time, the single column, dual elevator, Compact Twin, is extremely fast. That is one of the main reasons this model is becoming increasingly common in distribution environments.
A worker using this type of VLM can access over 100 tray presentations per hour to the golden picking zone. Depending on the line item affinity on orders, this VLM can deliver well over 200 lines per hour to a single operator using discrete order picking. Faster picking is possible using two or three VLMs with one operator. Tray and VLM slotting can be optimized to further increase speeds.
VLMs can incorporate different picking types such as batch picking, picking multiple orders simultaneously, to increase pick rates using software. By optimizing the sequencing orders by reviewing them for the line item affinity will generate the fastest picking speeds. Software can control how a VLM is zoned and/or optimized for slotting. The VLMs can be optimized overnight to have high use trays located closest to the opening (a process similar to defragmenting a hard drive).
The Vertical Lift Modules that offer the most storage density
The VLM machine that provides the most storage density is the Compact Double: single column, double deep, dual elevator VLM.
This double deep VLM has two racks of shelving in the front and two racks in the back of the elevator. This doubles the storage capacity of the VLM compared to the single lift. The storage footprint is very dense for this type of VLM as its footprint is low compared to each storage capacity.
The most common Vertical Lift Module options
To complement their basic functionality, VLMs can be tailored with additional options. VLMs can utilize technology such as pick-to-light systems or bar code confirmation systems. These technologies can help identify product locations and guide operators to specific cells and confirm picks and put-aways.
VLMs can be accessed at different levels and locations, such as floor grade, mezzanines, front, back, or front and back. Even the access opening itself can be specially configured for accepting pallets.
Lastly, there are also options for fire suppression, either with water or inert gas, and for climate control, including refrigeration.
Features to review when evaluating a VLM
VLM Drive Systems
One of the critical components of a VLM is the extractor drive system. The belt system, rack and pinion or gear system, or chain system drives a VLM machine. These vary in initial cost, reliability, maintainability, and life-cycle cost. Some systems use two points of contact for the tray load while others use a more stable 4 points construction.
VLMs that are built with rack and pinion drive and chain systems are particularly robust. Chain systems tend to be older and generate higher noise levels. The rack and pinion systems do not stretch and generally require less maintenance than belt drive systems.
VLM Software
Software is often a critical feature of any automated storage and retrieval system. The VLM software enables the various VLM capabilities, such as batch picking, storage optimization, and slotting optimization.
The VLM software should integrate smoothly and work with the existing Warehouse Management System (WMS) or Enterprise Resource Planning (ERP) system for maximum efficiency.
Start using Vertical Lift Modules (VLMs) Today
Adding the right VLM can dramatically improve the throughput, efficiency, and accuracy of your warehouse, distribution, or manufacturing environment.