Global Electronic and Computer Manufacturing Company Improves Picking Accuracy to Greater than 99% with Horizontal Carousels
Global Electronic and Computer Manufacturing Company Improves Picking Accuracy to Greater than 99% with Horizontal Carousels
Challenge
Challenge
One of the leading manufacturing companies for electronics and computer peripherals decided it was time to automate their warehouse and wanted to increase levels of throughput, storage density, and accuracy while also reducing space. With their New Jersey facility servicing all the parts requirements for 2400 authorized company service centers throughout North America and regions of South America, efficiently organizing inventory was essential.
Solution
Solution
By installing a single pod of four horizontal carousels and materials management, the company was able to replace standard shelving to streamline operations. Row after row of four-post shelving was replaced with a single pod of four horizontal carousels.
The pod contained more than 75% of the facility’s total inventory yet only occupied 30% of the floor space. The pod’s outer carousels each had 72 bins and the inner carousels 66 bins. Each carousel has 14 shelf levels. It occupies an area 12.8 feet tall and 80 feet long. A scissor lift in front of the carousels helps operators reach the bins easily.
Parts orders are downloaded from the company’s order entry system are sorted into batches of orders. The batches are optimized to minimize carousel rotation. Orders are picked into assigned totes. When the operator is ready to pick the orders, the carousels position themselves for picking. A LightreeΤΜ indicates the position of the SKU and quantity to pick. The operator then bags (if needed) and applies an adhesive label as it is place the SKU and the quantity.
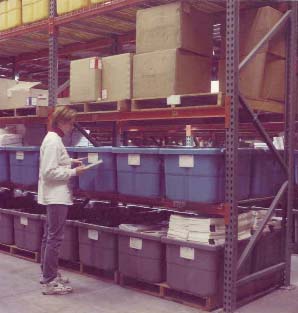
Results
Results
After installing the horizontal carousels, the company was able to immediately increase picking speeds from 35 lines per hour to 150 lines per hour, per person and reduced man hours by 75%. The carousels’ loading capacity proved 300% greater than previously used shelving systems, which allowed the company to reduce the size of their warehouse by more than 55%.
“White’s horizontal carousel system has provided a 15 month return on investment (ROI),” said the company’s parts department manager. The carousel system also helped improve picking accuracy to greater than 99% bettering the industry’s benchmark.
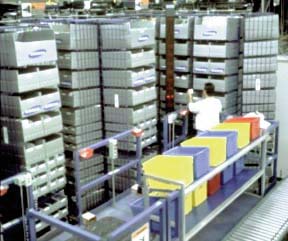
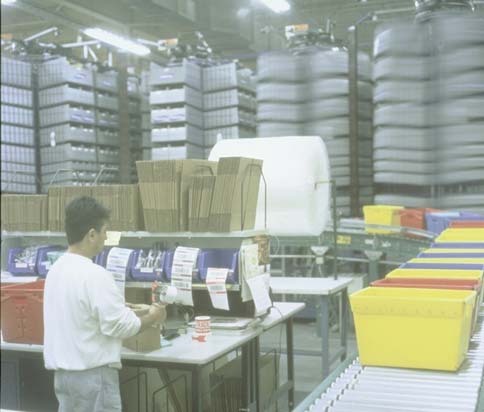
As the operator completes each pick they push a task complete button. As the operator completes each pick they push a task complete button. The previously picked carousel positions itself for the next pick. When all the picks in the batch are completed, the operator simply pushes the totes forward onto a waiting conveyor which delivers them to the packing station.
The parts distribution center supports the company’s entire product line, which includes over 2,000 models of consumer, business and information system electronic goods, such as VCRs, computer components, and TVs. At any one time 750,000 parts consisting of 20,000 SKUs must be in stock and ready to ship.
The parts development manager goes on to say, “Our pickers had to search the rows of shelving which was not only very time consuming but also very difficult to manage. Now an operator stands in front of the carousels and everything is brought to them, which is much more efficient.”
The implementation of the automated carousel system also allowed the same day shipping cut-off time to be extended from 2pm to 5pm. This additional three-hour window is important in helping the company keep their high level of customer satisfaction.