Transforming Warehouses: The Impact of Vertical Lift Modules
Transforming Warehouses: The Impact of Vertical Lift Modules
Byggplast & Båtprylar's Journey
Byggplast & Båtprylar's Journey
Since 2018, Byggplast & Båtprylar has revolutionized its inventory management by implementing seven Compact Twin vertical lift modules and a customized Compact Store solution. This transformation has expanded their unique product offerings from 7,000 to 9,000 items, with 4,000 of those stored in warehouse elevators.
The remaining 5,000 items are managed using traditional pallet racking within the same system. As a result, the need for overtime work has been eliminated, the demand for additional staff has decreased, control over inventory has improved significantly, and the number of errors has been minimized. Join them on this transformative journey.
Maximizing Warehouse Space
Maximizing Warehouse Space
Byggplast & Båtprylar Sverige AB is a key supplier to Seasea stores located from Malmö in the south to Luleå in the north. The chain comprises ten company-owned stores and 20 franchise locations. Additionally, the company supplies boat accessories to various boatyards, selected retailers, and directly to consumers viae-commerce. Byggplast & Båtprylar has been operating independently within the Hjertmans Group for several years.

The Company’s headquarters and warehouse are based in Segeltorp, conveniently located just off the E20 in Stockholm. This prime location houses the well-established boat accessories store, which has operated since 1979. The property encompasses a total area of 50,590 square feet, with approximately 32,291 square feet dedicated to the store, head office, and warehouse. Given the increasing sales and limited warehouse space, efficient utilization of every square feet is crucial.
Per Tengman, the Logistics and IT Manager, states: “We sell everything related to boating accessories, excluding the boats themselves, except for the occasional rubber dinghy. Interest in our products is strong, and we have consistently increased our sales every year.
Inventory Optimization with VLMs
Inventory Optimization with VLMs
“Choosing the Compact Twin was an easy decision. We were impressed by the twin function, which enables the lift to handle two load trays simultaneously. This doubles the picking speed, allowing us to pick from one tray while the system fetches the next.
Additionally, Weland Solutions delivered a great presentation, gave a professional impression, and were easy to communicate with. In 2018, we ordered the first three VLMs, and the positive impact was so significant that we added two more in 2020 and another two in 2021. With seven Compact Twins, we have achieved the most optimal storage solution for our range and limited storage space, and we are very satisfied,” says Per.
Thorough Preparation Yields Results
Thorough Preparation Yields Results
“Preparation is key for integrating VLMs into warehouse management efficiently. Peter from Weland Solutions visited us beforehand to assess which items would fit where. The decision of what goes into the warehouse Vertical Lift Modules depends on size, weight, frequency, and theft potential,” explains Per.
“It’s important to understand that the company must put in the effort to integrate a warehouse lift. We started by categorizing all items sold into A, B, and C categories and physically verifying their sizes to ensure they fit properly on the loading trays. We completed this work before the VLMs arrived,” advises Per.

“Today, we store everything from small screws to exclusive autopilots as big as moving boxes in the VLMs. We’ve increased picking speed by organizing items based on tray hits. We initially used simple corrugated cardboard boxes for the cargo trays, thinking we’d need to change them later, but they’ve held up well,” notes Per with a smile.
Change Takes Time
Change Takes Time
“The staff’s initial apprehension about the new system and how it would work was a significant challenge. Despite their doubts, everyone adapted quickly and is now very positive,” says Per. “However, it’s essential to be patient, as moving items into the VLMs takes time while maintaining regular operations.”
The first three lifts took about 1.5 months, but subsequent ones only took about 3 weeks. We developed pick lists for VLM deliveries, alternating items in phases. Now, deliveries from outside go directly into the VLMs to ensure a balanced inventory. We also maintain ample storage on conveyor belts to guarantee back-to-front replenishment,” explains Per.
Benefits of a Unified Warehouse System
Benefits of a Unified Warehouse System
“Initially, we only used Compact Store for the lifts. In 2020, with a specially adapted solution, we expanded its use to include pallet rack items as well. This eliminated the need for paper-based pick lists and allowed us to manage orders digitally, covering racks and VLMs. Integrating Compact Store with our M3 business system automatically registers all picking. We even included pictures of each item in the system for easy identification.
Thanks to this integration, errors in picking from pallet racks have been minimized, making a significant difference,” says Per happily. “Our warehouse is now highly efficient, divided into three zones: Zone 1 for smaller items, Zone 2 for heavier truckloads, and Zone 3, which houses our seven Compact Twins. A significant advantage is the ability to process multiple orders simultaneously, which wasn’t possible with the paper system. Order scan be picked from all zones and consolidated into large cartons during packing. The system guides the picker on where to start, optimizing the picking loop for minimal steps. This setup saves us considerable time and effort, with 40% of our picking now done from the VLMs,” shares Per.
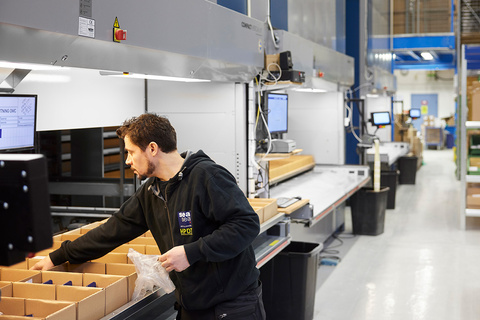
Optimizing Inventory Handling with a Smaller Team
Optimizing Inventory Handling with a Smaller Team
“Beyond expanding our product range, we can manage our high season with fewer seasonal employees than before. Despite this, our staff no longer need to work overtime, which was common previously. Today, one person can do the work of three, and if needed, we can assign one more person to the VLMs to double the output while maintaining efficiency,” concludes Per with a smile.